Tanking failure, a sorry tale indeed
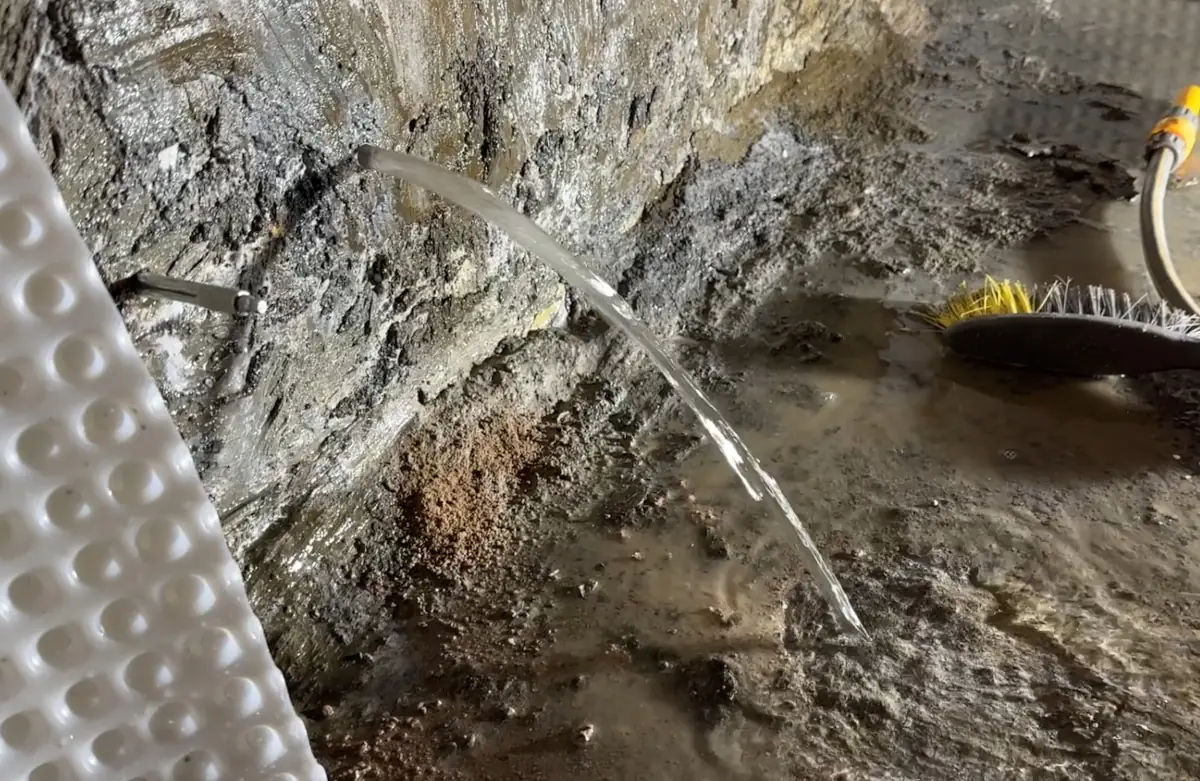

Tanking failure, a sorry tale indeed
This blog post examines a case where a basement waterproofing system failed after a materials supplier reduced the scope of the initial waterproofing design put forward by the project Architect, and suggested a contractor to install measures. When the basement became damp, and in the words of the client, it became a sorry tale indeed.
The Architects waterproofing design was passed to a specialist materials supplier
The supplier changed the design to a single system - internal slurry tanking
The supplier recommended a contractor to install the slurry tanking
It was an innapropriate design for the structure (masonry) and site conditions (high water table)
The original waterproofing design intent for the basement, shown on the Architects drawings, was two forms of waterproofing, external and internal tanking barriers. This is typical in new build waterproofing for habitable space, in that it follows the guidance within British Standard 8102 Protection of below ground structures against water from the ground, in relation to 'combined protection', which is the use of two forms of waterproofing, either where it's very wet (which this site was) or the consequences of failure are significant (which they were).
The structural design included masonry retaining walls, which do not suit the site conditions, or ideally the use of external and internal tanking systems, but notwithstanding, when the project Builder passed the drawings to a specialist waterproofing supplier, for reasons unknown they reduced the specification to a single form of waterproofing (internal slurry tanking), and did not pass comment on the structure. They also suggested an installer.
Work progressed in line with the supplier's recommendations and the house was completed.
Initially the issues of dampness were suggested by the supplier as being associated with the plumbing installation, but issues persisted and Trace were approached to advise and report.
We identified that it was a wet site from inspection of the land drain arrangement and in discussions with the builder who was very helpful, and understandably mortified, that it was a masonry retaining wall with a single form of protection, that being a cementitiou slurry tanking material, that had been installed by a waterproofing specialist that had been put forward by the materials supplier.
Trace produced a report with a detailed analysis of the design in relation to best practice British Standard guidance, and advised that ultimately it would be necessary to expose the structure, in order to understand the probable source of water within the floor construction. This was progressed by the builder, who fully stripped out the insulation, screed, and the bottom half of the dry lined retaining walls.
Upon stripping out, there was one particular area of water ingress, although it was not the only location in which there were leaks. Trace undertook localised resin injection and barrier tanking works, but have ultimately protected the space by installing a cavity drainage waterproofing system, comprising drainage channels, cavity membrane and a sump pump system, so we can guarantee that this is now a dry space.
So what went wrong?
The supplier clearly didn't follow the design process detailed within BS8102:
- Inadequate consideration of site conditions - the site investigation report should have been reviewed to identify a high risk site
- The masonry retaining walls, which are deemed inherantly high risk in BS8102, were not ideal in site conditions.
- The use of sub-surface land drainage given the site conditions were unlikely to provide much benefit.
- The waterproofing would have to be perfect to function, so does not assume risk of defects as per BS8102 guidance.
- The waterproofing was behind and beneath insulation, plasterboard, screed, under-floor heating, so there no easy or practical strategy for repair.
In my 24 years of basement waterproofing, I have not seen many cases of evident negligence as I have within this case. Notwithstanding, when challenged, the suppliers just blamed the installer, whom they had recommended. That installer had no insurances in place to cover issue with their work (as we have) and being a small entity (nothing wrong with that but not perhaps appropriate for this stature of work) essentially stated that they would have to close their business if pursued.
It is common practice in the event of a new basement being considered, to approach a material supplier for advice. There is no issue with this but understand what you get and what you do not get.
It is important in the first instance that the waterproofing design is produced by a qualified waterproofing designer, who is specifically appointed, and is taking the design responsibility for the waterproofing onto the professional indemnity insurance. This is as aspect which must be clarified on any project, in that just because a supplier (for example), has the professional indemnity cover, it does not mean that they will accept design responsibility. Usually they intend for the responsibility to be passed to another specifier, such as the Architect, and they act as a 'waterproofing specialist' (a term from BS8102), but not as the actual 'Waterproofing Designer'.
Liability and performance are closely interlinked, we are all busy and so whether intentional or not, there will always be lesser attention to projects where ultimately there is no responsibility and liability. Suppliers who do not design, and do not install, in essence have very little liability.
The better suppliers will steer those that enquire towards reputable and capable contractors, but ultimately these companies can only grow their businesses through selling more materials and even with our preferred suppliers, we've recently had experience of being asked to quote where supposed specialists from their 'approved list' had installed membrane onto walls the wrong way around!
In brief, the ideal is an installer who also takes the design responsibility and then provides a single point of responsibility for the waterproofing.
- Look for professional indemnity insured design (by the installer) where they are specifically stating that they take the design responsibility.
- Product guarantee insurance (by the installer, where their 'product' is their installation).
- Experience and competence relevant to the size and complexity of the project.
- Ask for specimen guarantees and copies of their terms.
- Assess the quality of the correspondence (design drawings and associated reports).
- That the processes within BS8102 are referenced and followed.
This is very much what we do.
Other recent projects
Experts in Structural Waterproofing & Timber Repair
Trace are Industry leading waterproofing contractors
Get in touch