Damp Proofing Specialists
Whether you're dealing with a persistent damp problem, renovating a period property, or need a breathable solution, Trace Remedial are your local specialists in issues of dampness in buildings.
Get in touch

Trusted Damp Proofing and Lime Plaster experts in Manchester
At Trace Remedial, we bring decades of experience to every damp issue we solve. From solid brick terraces to timber-framed cottages, we know each structure reacts differently to moisture, so your solution needs to be tailored.
We assess your building’s construction and materials to understand how damp behaves and choose the most suitable method to manage it. For heritage buildings, our breathable materials like lime plaster work with the property’s natural characteristics. Our reputation is built on accurate diagnostics and long-lasting results.
Trace are industry leading experts in damp and the effect of moisture on buildings
Get in touch
Accredited Professionals
At Trace we have chartered MRICS and Property Care Association (PCA) accredited Surveyors experienced in all areas of dampness in buildings, from insect attack to timber decay to issues of moisture above and below ground, and building regulations compliant design for dwelling ventilation.
Award-Winning Service
We’ve earned multiple awards across the North West for our clear advice, responsive service, and reliable long-term results. As a TrustMark-registered business, we meet government-endorsed standards you can trust.
Trusted by Professionals
Architects, conservation officers, and property developers regularly choose us for our detailed surveys, precise diagnosis, and proven remedial solutions. Whether it’s a listed building or a new extension, we bring decades of practical, professional experience to every project.
Free Damp Proofing initial consultation
Get in touch with our team. We are trained, certified, and up to date with the latest industry standards, including the RICS/Historic England/PCA joint position statement on the investigation of moisture and its effects on traditional buildings.
Find out more
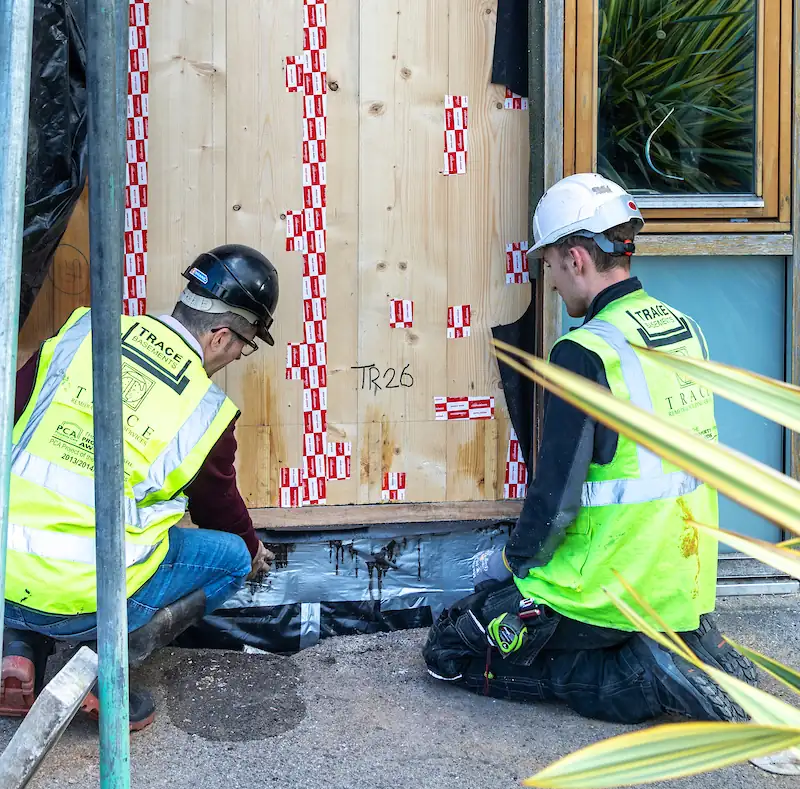
Accurate diagnosis is at the heart of what we do
Measurement of moisture
Trace can undertake quantitative moisture measurement in structures employing intrusive methods of calcium carbide speedy meter testing, gravimetrics (the oven dry method), and non-intrusive electronic moisture meter testing, in timber and with due consideration in other materials. We understand the limitations and advantages of each method and employ them accordingly.
Drone Surveys
Trace are licenced and insured to complete drone surveys, facilitating visual access to otherwise difficult to access areas of roofs, chimneys and associated detailing.
Other Tools
LiDAR scanning is a method of capturing and displaying a three dimensional representation of the interior and exterior of a building for reference and reporting purposes. We are happy to share this information with our clients if that should assist them with other uses.
Thermal imaging cameras are employed to measure differential temperatures to aid in our assessment of conditions.
In structures new and old, assessment can often be a systematic approach, whereby obvious defects may be addressed and conditions monitored to prove or disprove the relationship with the visible symptoms.
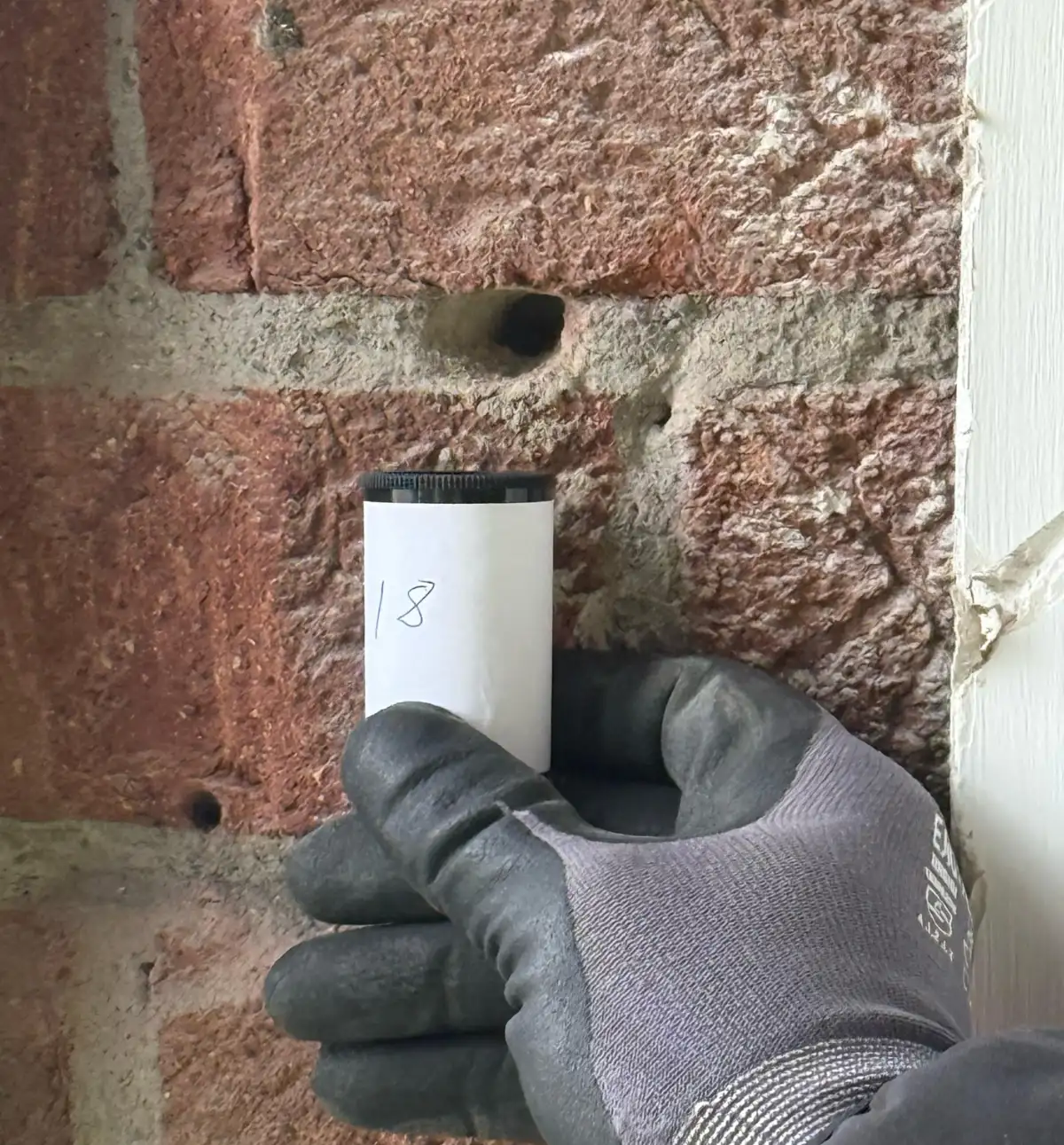
Common causes of damp we treat
- Leaking drains and pipes
- Bridging plaster or render over DPC
- Faulty or shallow injection DPCs
- Hygroscopic salt contamination
- Poor ventilation and condensation build-up
- Renovation mistakes (e.g. tanking systems that trap moisture)
Leading experts in damp and the effect of moisture on buildings
Get in touch
Trace Damp Proofing Processes
Free Initial Consultation
We assess the damp symptoms, check for common bridging issues, and identify whether your DPC is functioning or has failed.
Tailored Recommendation
We advise on the best solution, whether it's installing a new chemical DPC, cutting back bridging plaster, or applying a breathable lime plaster system.
Get in touch
Expert Application
Our team handles every stage professionally, from damp course injection to lime plastering, ensuring breathability and compliance with conservation standards where needed.
Learn more
Aftercare & Monitoring
We guide you through post-treatment care including drying times, decorating advice, and maintenance tips.
Learn more
Damp walls, a holistic approach
Breathable Lime Plaster
This natural method is ideal for traditionally built solid walled homes, helping damp walls dry out while forming a breathable and persistently vapour permeable internal build-up. While the plaster in isolation does not address the source or root cause of the dampness (which is assessed as a part of the survey and design process), it allows for moisture accessing the walls to be lost to the interior where ventilation allows for loss to the exterior.
find out more
Modern Damp Proofing Methods
Modern methods include the installation of retrofit injection damp proof courses. These materials are derived from silicone, which is a polymer and in this regard comparable with the many other many other man-made polymer materials employed within our homes. They are totally inert and form a ‘pore-liner’ which repels water, rather than water being able to adhere to pore and capillaries, and as such capillary action - that which allows moisture to rise, is defeated.
Damp proof courses are usually combined with physical membranes, which then isolate new internal finishes. The rationale with this approach is that the internal finish can be guaranteed to be blemish free, whilst the structure dies down behind, in the absence of further rise of moisture (addressed by the DPC).
Get in touch
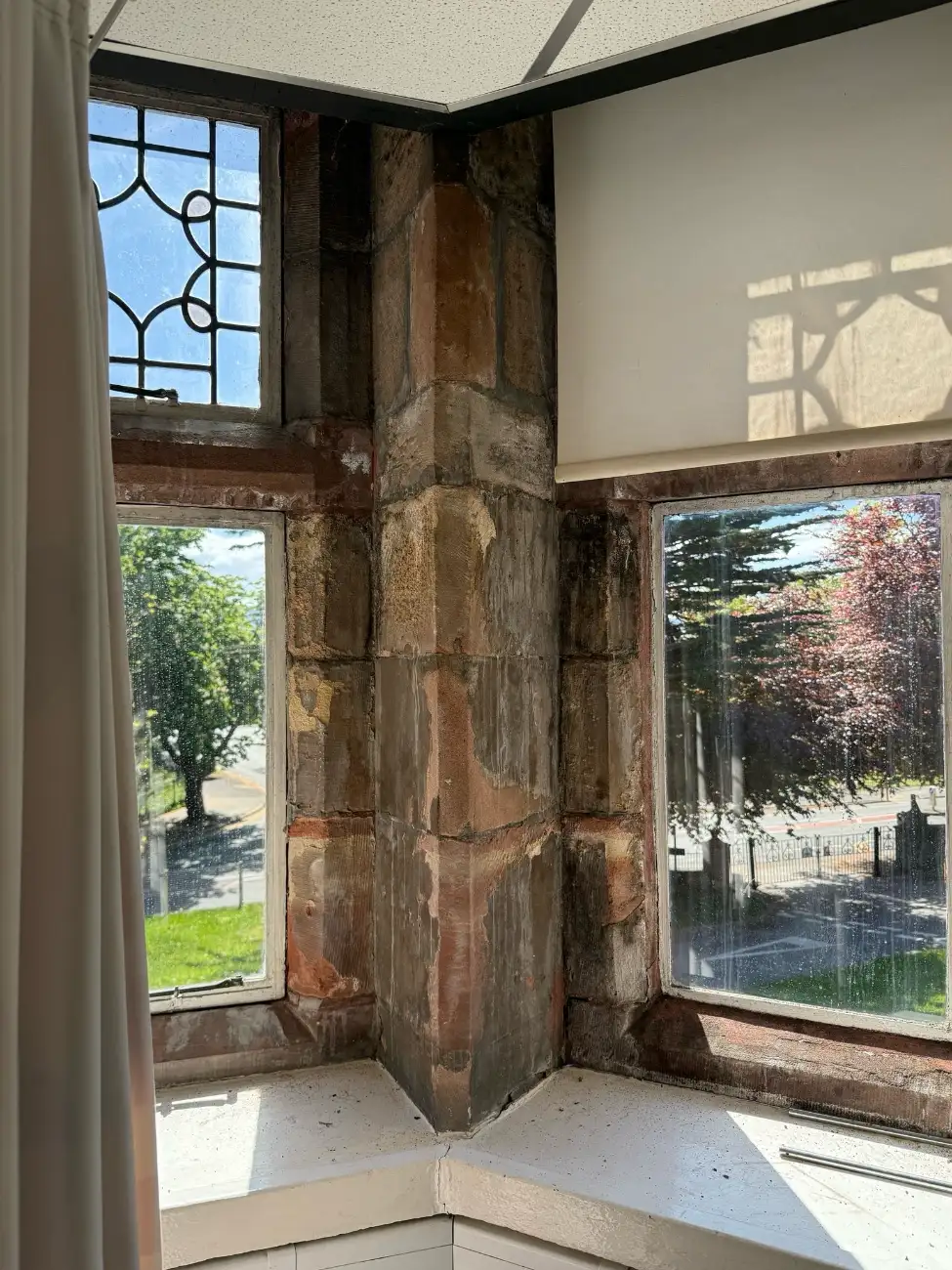
Winning awards & Accreditations
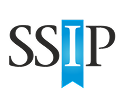
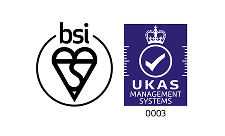
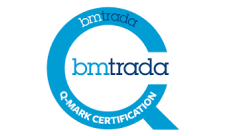
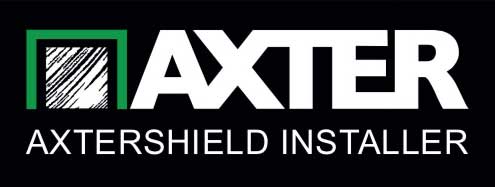
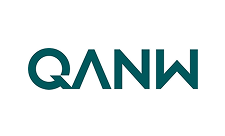
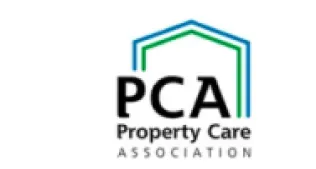
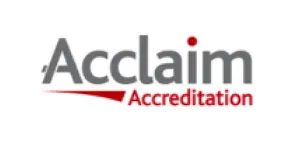
.webp)