Procuring basement waterproofing
Managing risk is crucial in structural waterproofing. No client or consultant wants to deal with problems, even with advancements in materials, design, and installation. Choosing the right approach can be confusing due to varying advice in the market.
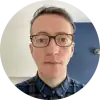
By James Hockey
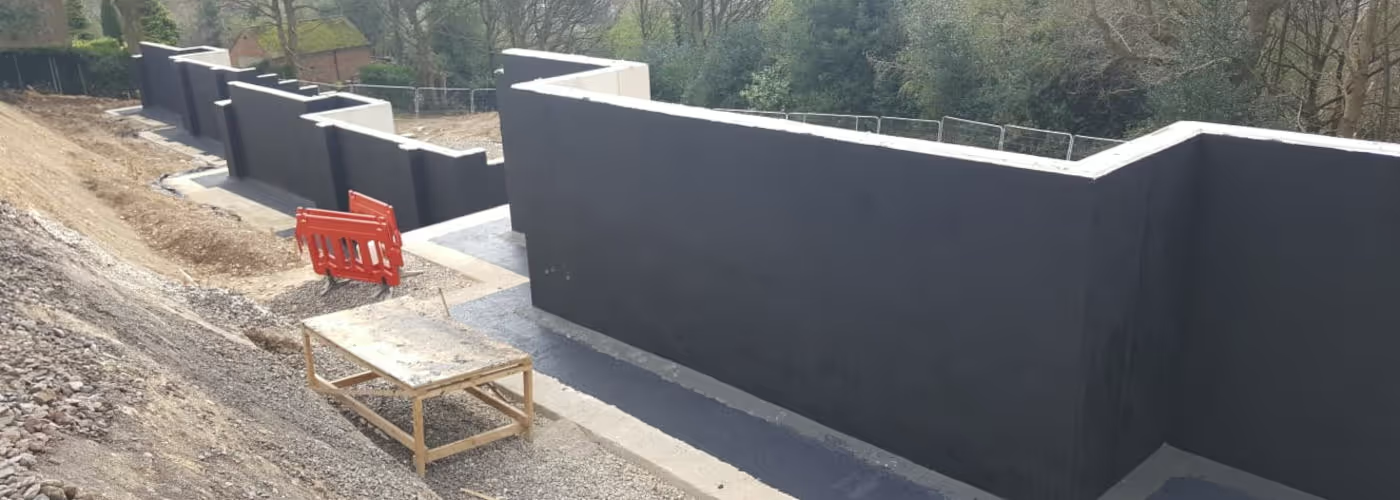
This article aims to break down different market options and their implications. However, we write as a contractor specialising in waterproofing design and installation, so our perspective may have commercial bias. Our market understanding, based on experience, might not be entirely accurate.
To provide a broader analysis, we conducted an industry survey on various topics, including roles, insurance, and design preferences. This analysis is based on the survey results.
The following is an article I wrote for the Journal of Building Survey, Appraisal & Valuation - copyright: https://www.henrystewartpublications.com/jbsav
Bio
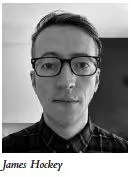
James is a Waterproofing Design Specialist and Structural Waterproofing Contractor (Trace Basements) with over twenty years’ experience in dealing with a wide variety of basement scenarios from small scale residential to large scale and deep commercial basement construction, with a focus on problem basement investigation and remedial works. In 2021 James was one of two UK Contractors serving on the update panel for BS8102 Protection of below ground structures against water ingress, since published in 2022.
Survey Methodology and Sample:
The survey primarily targeted industry colleagues through direct contact, LinkedIn groups, and the Property Care Association (PCA) email distribution. The PCA represents a significant portion of the industry, including major manufacturers, installers, and independent professionals.
Sample Focus:
The sample primarily consists of professionals involved in waterproofing occupied basements (e.g., car parks, plant rooms, storage, habitable spaces). Tunnel waterproofing is less likely to be a focus for most respondents, especially contractors and independents.
Qualifications:
While the sample size is relatively small (59 respondents), nearly all hold relevant qualifications (CSSW or WDS). This ensures that the data comes from highly qualified professionals with extensive experience in the field. The high representation of WDS-qualified individuals (the highest level of specialist qualification) further strengthens the quality of the sample.
British Standard 8102:2022:
The principal design guidance for basement waterproofing in the UK is BS8102:2022. This standard recommends the appointment of a 'Waterproofing Specialist' within the design team, who should be suitably qualified and experienced. Importantly, it distinguishes between the 'Waterproofing Specialist,' who provides advice, and the 'Waterproofing Designer,' who takes responsibility for the waterproofing design and insures it with their professional indemnity insurance. This distinction can often lead to confusion for project stakeholders.
Providers:
Our survey categorised Waterproofing Specialists and/or Designers into three groups:
- Independent Waterproofing Surveyor/Designer: These professionals provide advice and design services but do not supply or install waterproofing materials.
- Surveyor/Designer working for a Contractor: These individuals work for companies that install waterproofing systems and may also provide design services.
- Waterproofing Materials Supplier/Manufacturer: These companies supply waterproofing materials and may offer design support and technical advice.
Each group answered the same questions, covering:
- CSSW qualification/WDS registration
- Level of design input provided
- Professional indemnity insurance coverage
- Design preferences for new builds
- Design preferences for existing structures
Comparing answers reveals the services offered and their implications for stakeholders. Additionally, we can analyse how roles influence system design preferences, a key question for design teams.
Design Input:
The level of detail provided in waterproofing designs varies among different respondents. Independents primarily offer bespoke drawings and written specifications based on provided architectural/engineering drawings.
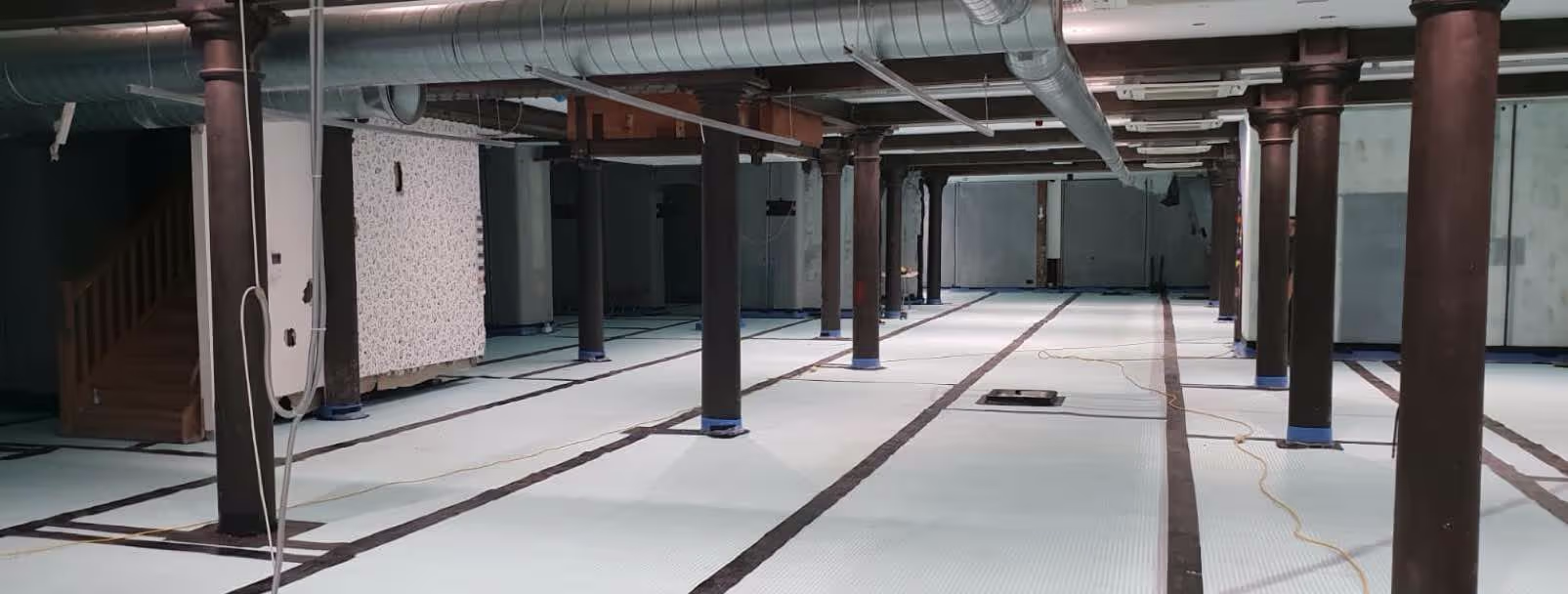
Contractors have a mixed approach, with around 45% not developing a detailed design in advance and instead designing on-site as work progresses. This might be suitable for smaller contractors or projects within existing structures, where assumptions and design adjustments are necessary during construction.
However, producing bespoke designs and specifications in advance is considered ideal for achieving optimal results, especially for more complex projects. This approach also allows contractors to take full responsibility for the design and installation, offering a single point of liability and ensuring better quality control.
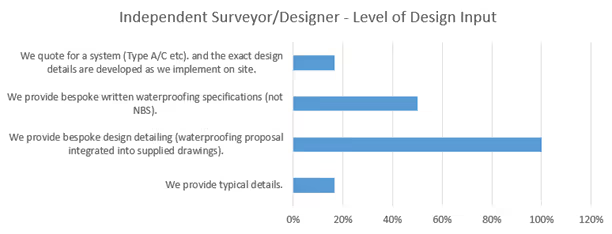
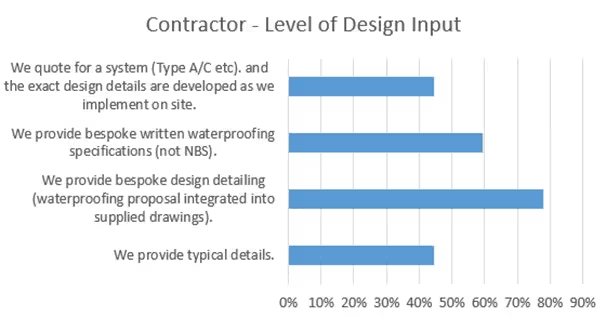
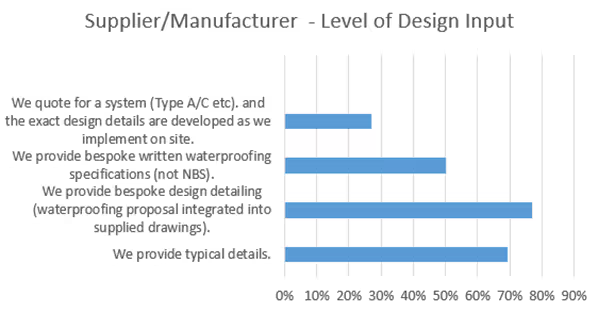
Professional Indemnity Insurance (PII) and Design Responsibility in Waterproofing
BS8102 (2022) recommends including a "waterproofing specialist" in the design team. However, this specialist may not always act as the "waterproofing designer" who takes ultimate design responsibility and whose PII covers the design.
Companies may carry PII to cover their advice, but not necessarily take design responsibility. This can be confusing for design teams and stakeholders.
Survey Results:
- Independents: Mostly take full design responsibility, likely producing designs themselves. Some advise clients to employ specialist installers with PII, avoiding split liabilities where design and installation are separate.
- Contractors: A small proportion have no PII and design their own work, potentially risky for larger projects. Some carry PII for advice but not design, leading to split liabilities. The majority offer PII for design selectively, based on project size. However, taking design responsibility and installing avoids split liabilities and benefits all stakeholders.
- Suppliers: None take full design responsibility on every project. Some have no PII and design responsibility always rests with others, a traditional model. Others offer PII but design responsibility is with a third party. Some offer PII based on project size or fee.
Overall, the survey reveals varied approaches to PII and design responsibility in the waterproofing industry. Understanding these differences is crucial for effective risk management and ensuring successful project outcomes.
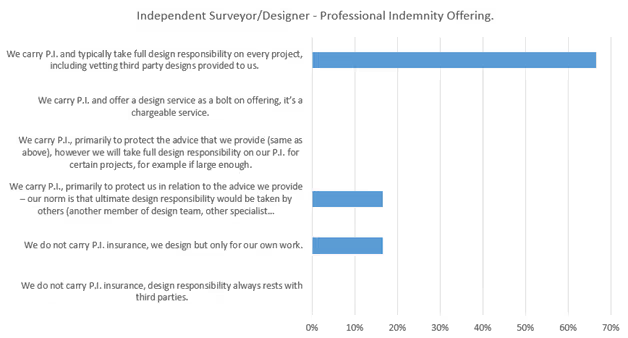
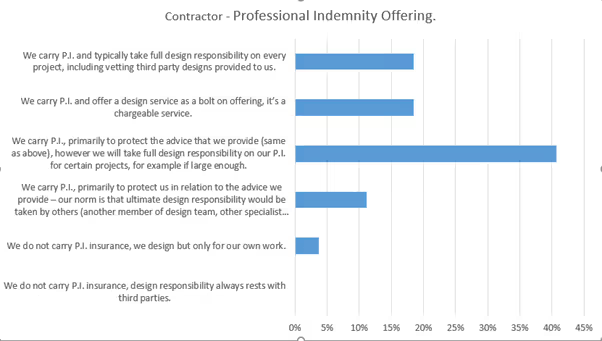
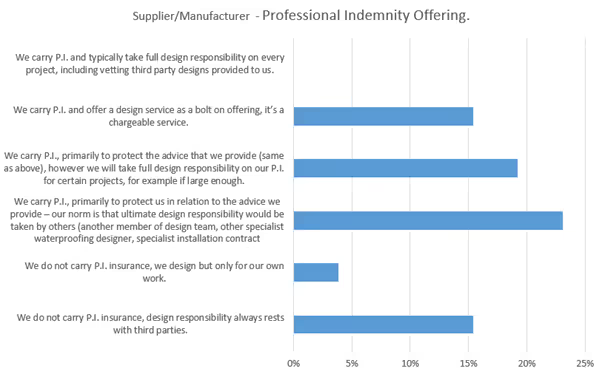
Basement Waterproofing Design Preferences in New Construction:
Scenario: A high-risk (wet) site with a concrete structure, a water table above basement slab level for extended periods, and intended habitable use with typical fit-out (grade 3).
Options:
- Type A: Tanking (physical barrier to block water)
- Type B: Integrally waterproof structure (structure itself blocks water)
- Type C: Cavity drainage (system collects and removes penetrating water)
Combined Protection (BS8102 6.2.3): Using dual waterproofing types where risks or consequences of failure are significant. This approach has become more common, encouraged by warranty providers due to past basement waterproofing issues.
Survey Results:
- Independents and Contractors: Prefer combining barriers (A or B) with Type C cavity drainage. Contractors slightly favour Type A over Type B.
- Suppliers: Show a wider range of preferences, with combined A & C being the most popular choice.
Conclusion: The survey indicates a clear industry preference for combined protection systems in high-risk basement scenarios, particularly those combining a barrier (Type A or B) with cavity drainage (Type C).
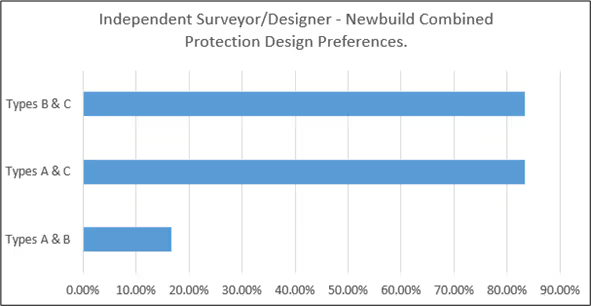
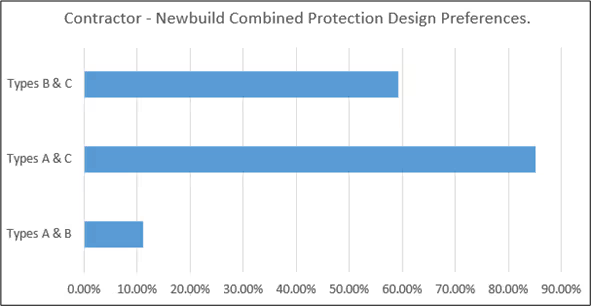
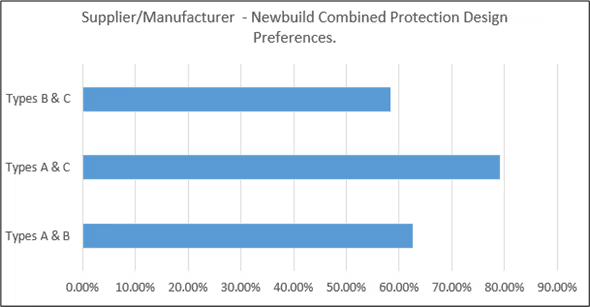
Basement Waterproofing Design Preferences in Existing Structures:
Scenario: A residential basement conversion (grade 3) in a detached masonry structure in good condition, located on a lower risk site with no history of water ingress. There's an option to upgrade the floor slab for internal Type A, but insufficient space for Type B.
Options:
- Type A: Tanking (physical barrier to block water)
- Type C: Cavity drainage (system collects and removes penetrating water)
- Type A & C combined: Combined protection approach
Survey Results:
- Independents and Contractors: Mostly prefer Type C cavity drainage alone or combined with Type A tanking. Only a small proportion would propose Type A tanking alone.
Conclusion: In existing structures, there's a clear preference for Type C cavity drainage, either as a standalone system or combined with Type A tanking. Type A alone is less favoured, likely due to the limitations and challenges of applying tanking in existing structures.
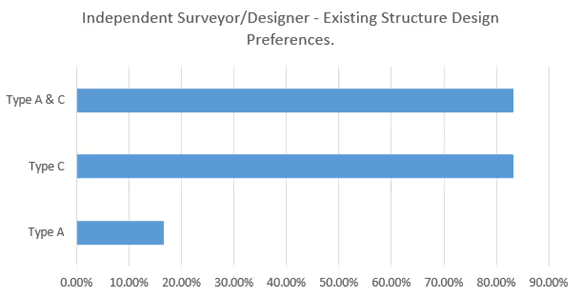
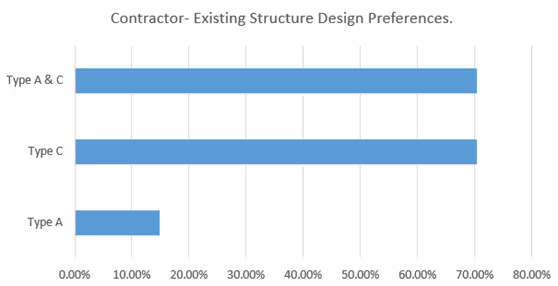
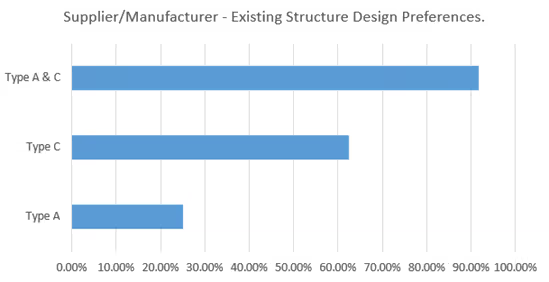
Design Preference Analysis:
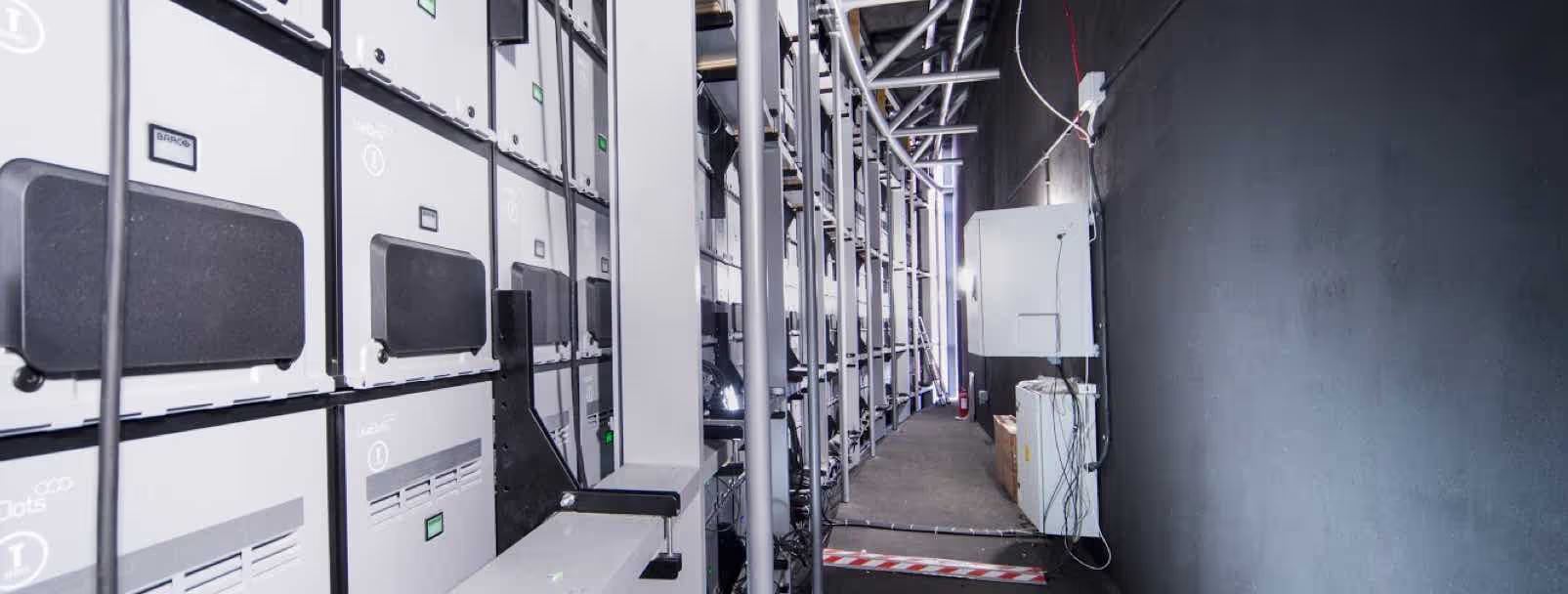
Factors influencing design recommendations:
- Risk aversion: Desire to avoid failures due to potential liabilities and costs.
- Liability: Responsibility for design and installation, and the potential financial implications of failures.
- Commercial factors: Financial incentives related to promoting specific products or services.
Risk aversion and concealed structures:
- Waterproofing in habitable spaces is often concealed, making defect location and repair difficult.
- Type C cavity drainage relies on drainage, reducing the impact of minor membrane defects.
- Type A and B barrier systems require a perfect installation to prevent leaks under pressure, making them higher risk for concealed structures.
Liability and risk aversion:
- Independents mostly take design liability, with no installation liability, and tend to be more risk-averse.
- Contractors always have installation liability and may have design liability, potentially influenced by commercial factors related to installation profits and control over the waterproofing process.
- Suppliers may or may not take design responsibility, have no installation liability, and often offer a wider range of products, potentially leading to lesser risk aversion and a wider acceptance of different system configurations.
Conclusion:
Design preferences are influenced by risk aversion, liability, and commercial factors. Independents and contractors tend to be more risk-averse due to their liability, favouring Type C cavity drainage for concealed structures. Suppliers, with lesser liability, may be more open to various system configurations.
Tendering and Procurement:
The tender process doesn't always yield ideal outcomes, but design standards are improving. Pricing waterproofing requires a thorough understanding of the project, ideally with a detailed design matching what the contractor would install and guarantee.
As a contractor taking design responsibility, influencing or altering designs at the tender stage is often difficult, leading to potential walk-aways or split liabilities with the designer, which isn't optimal for the client.
Options for design and procurement:
- Contractor design: Pay a competent contractor to design and guarantee the waterproofing. If the price is unsatisfactory, another contractor with PII can adopt the design.
- Independent design: The independent creates the design, and the contractor with PII adopts it. This sets a high bar for the installer but may be costly.
- Registered contractor schemes: Suppliers with registered contractors who can take design responsibility and adopt their designs offer a solution. However, scheme quality varies, and some may prioritise maintaining a customer network over competency.
Ultimately, quality comes at a price. Value is important, but prioritising the lowest cost can lead to cut corners and compromised quality. The right design with sufficient detail is crucial.
Key takeaways:
- Understand what each service provider offers, particularly regarding design input and PII coverage.
- The "Waterproofing Specialist" may not be the "Waterproofing Designer" taking ultimate design responsibility.
- There's a clear preference for including Type C cavity drainage in new and existing builds, especially among independents and contractors.
- Commercial influence and liability levels may impact design preferences, with suppliers potentially being more open to riskier configurations due to lower liability.
- Avoiding split liabilities is optimal, ideally with a contractor taking ultimate design responsibility, even if the design intent is developed by an independent.
In conclusion, understanding the intricacies of design, procurement, and liability is crucial for successful waterproofing projects. Prioritising quality and avoiding split liabilities can lead to better outcomes for all stakeholders.
References: