Guide to Basement Structures and Waterproofing
Basement structures can be formed using varied methods and materials, each with implication upon resistance (or otherwise) to groundwater penetration, which in turn has an implication on the waterproofing design, with this also being influenced by proposed usage and site conditions.
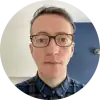
By James Hockey
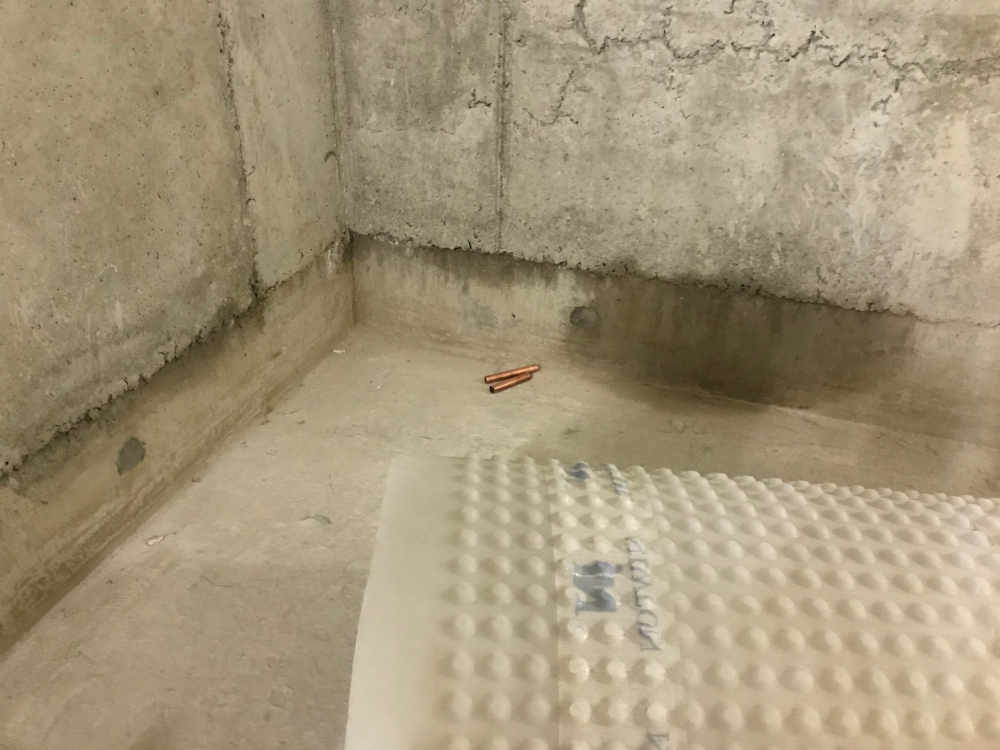
If it sounds complicated, not to worry, focus primarily on the fact that different structures provide different levels of resistance to penetration, and that this is one part of that which should be considered in producing a waterproofing design.
The most common basement structures that we see involve open excavations and reinforced concrete rafts ('monolithic' foundations extending fully beneath the basement footprint) which are formed first, before retaining walls are formed, which bear onto the raft either in reinforced concrete (cast on-site), or 'reinforced masonry'.
Cast in-situ concrete walls are formed (onto the raft) by erecting shuttering with steel reinforcement placed into this, then pouring concrete into the shuttering, resulting in a 'solid' concrete wall.
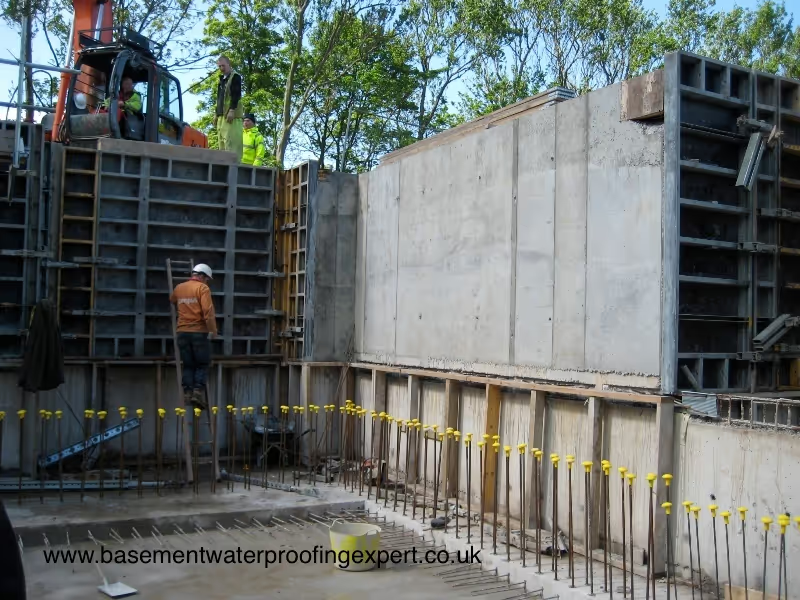
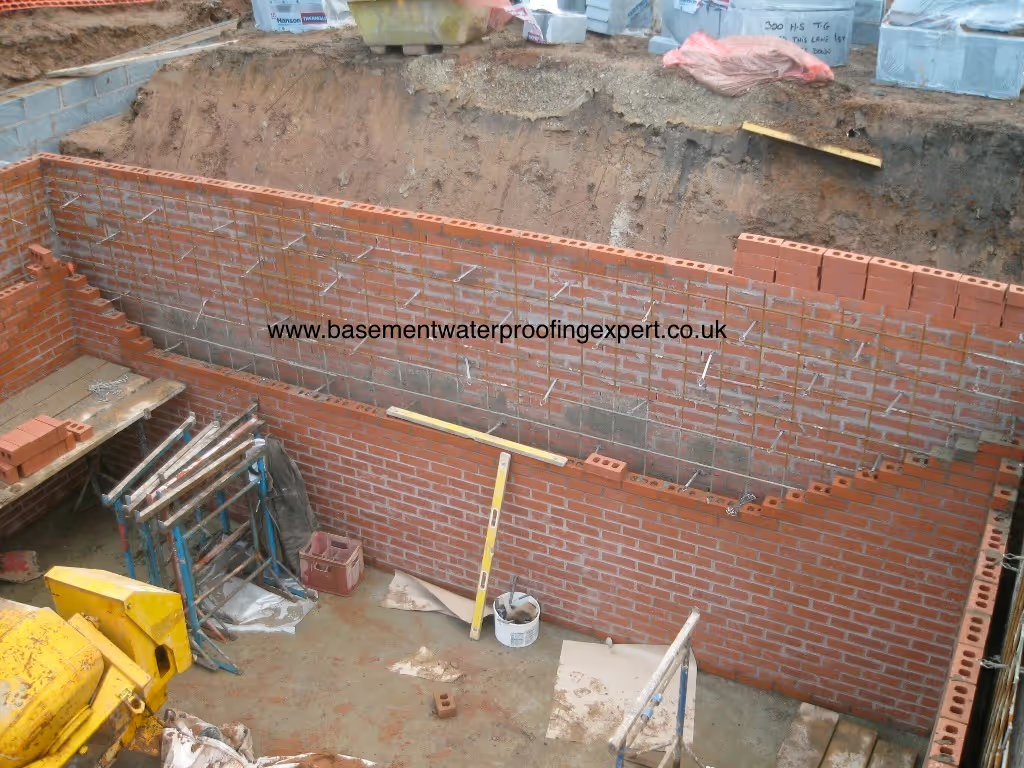
Beyond the above we also see embedded retaining walls which can avoid the requirement for an open excavation, in that piles (steel or concrete) are driven or bored top down, this forming the retaining walls, with the ground internal of those then being excavated, and with this approach the concrete slab is formed after the walls.
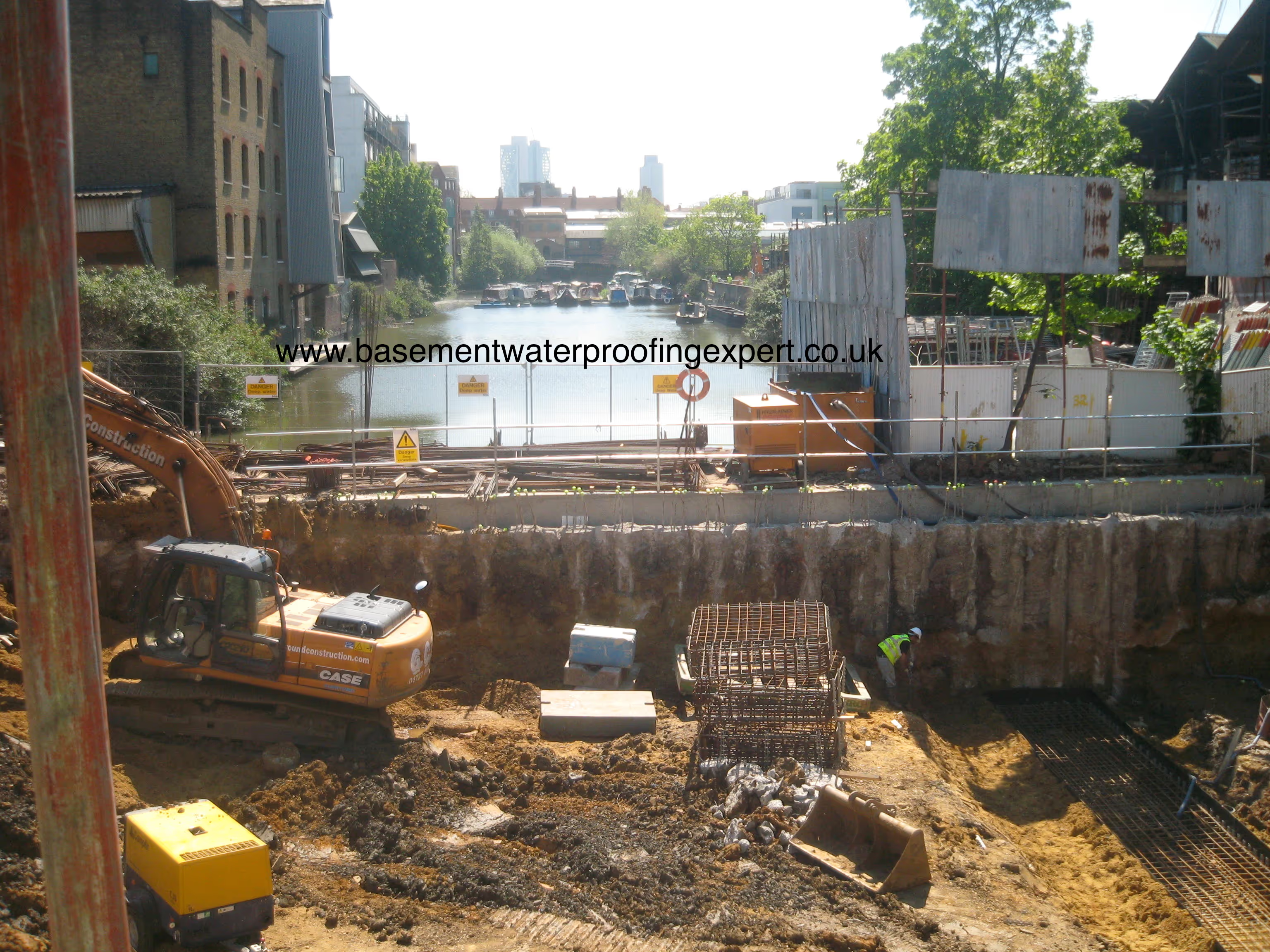
There are other methods/structures which generally we see less of, such as precast systems where concrete wall panels are manufactured off-site, then delivered to site where they are craned into position (over a raft) and fixed together.
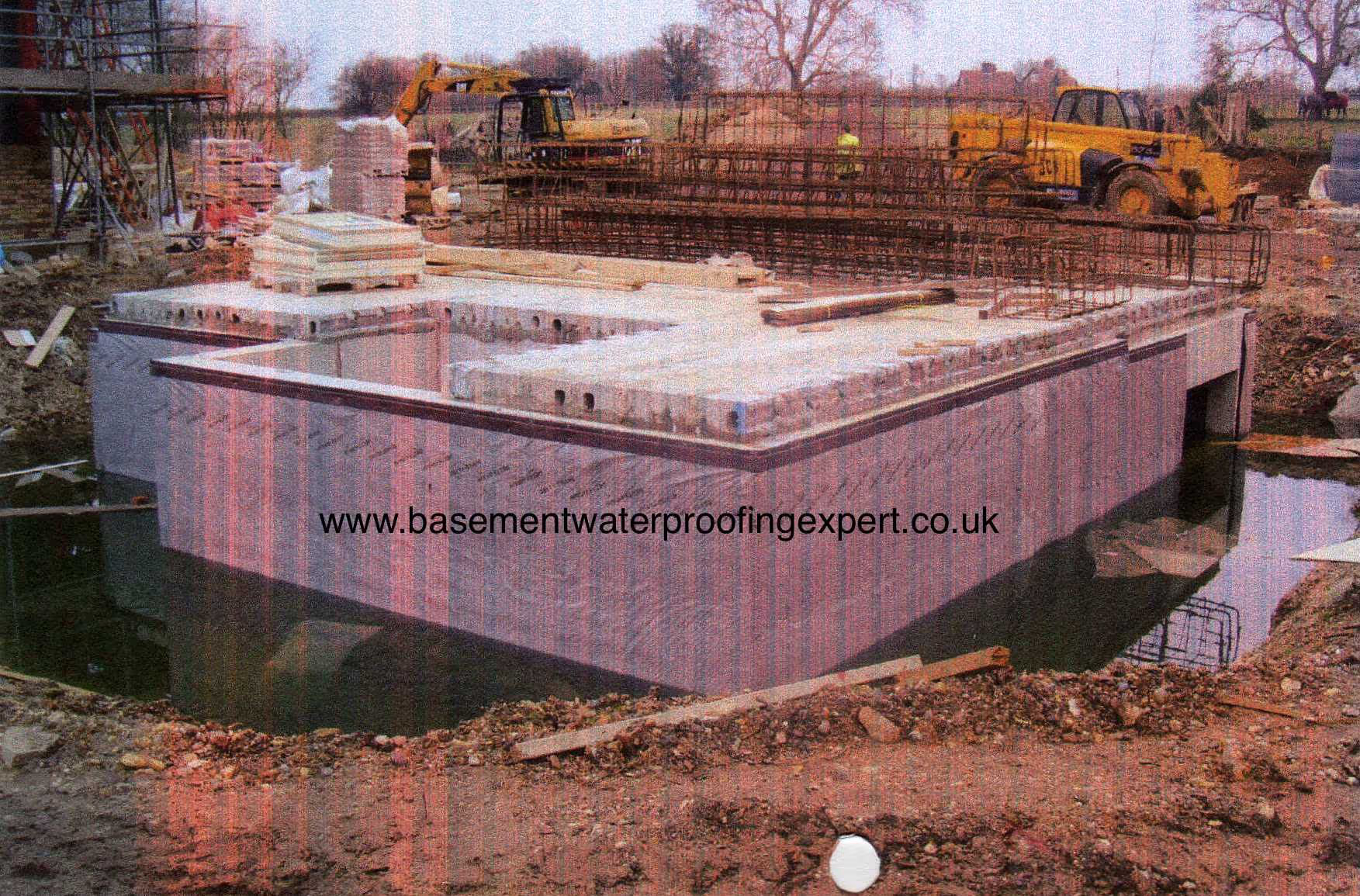
ICF (insulated concrete formwork) is another approach, this being a hollow polystyrene block wall system, which is placed lego fashion (sorry ICF people) over a raft - or at least in basements they should be used with a raft - and then filled with concrete/reinforcement. It acts as a permanent shuttering system with the polystyrene component providing the wall insulation.
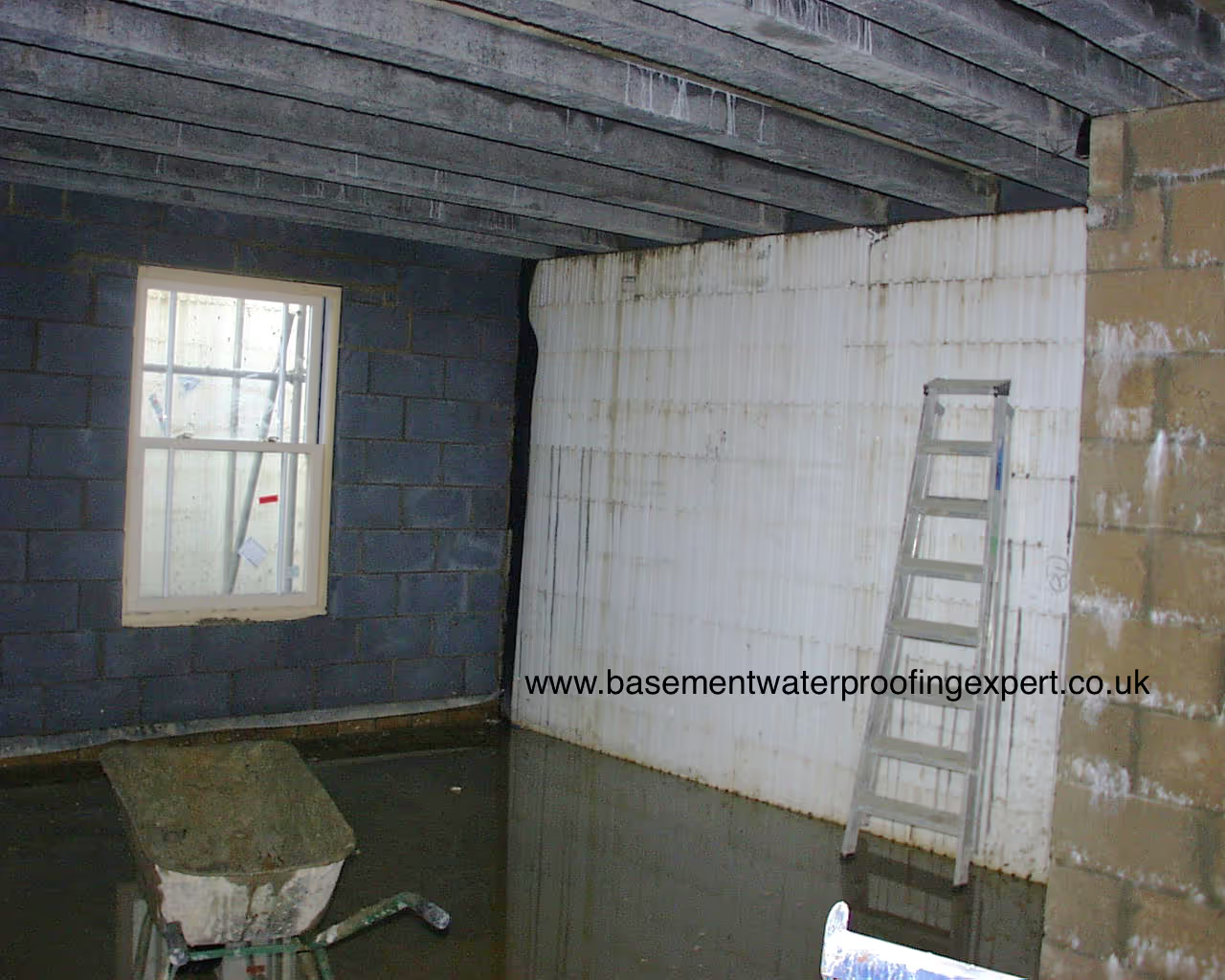
NB: The 2022 revision of BS8102 Protection of below ground structures against water ingress, includes commentary that forms of modular construction including ICF are considered to be inherently high risk. It is not a system hugely liked by those of us that provide long term comprehensive guarantees.
There are also concrete block systems which function like ICF in the way in which they built up, and in that they provide a permanent shuttering in which to place concrete and steel, essentially this is another form of reinforced masonry.
From a waterproofing perspective, it is a case firstly of understanding how permeable a given structure will be, and then importantly how it will interact with the proposed waterproofing.
Generally, less permeable structures are advantageous in that it makes the task of limiting scope for penetration easier, and while you can effectively waterproof any form of structure with appropriate design and installation, if we were dealing with aggressive sites (very wet), we would avoid certain forms of structure.
So, scope for penetration...
Concrete is an inherently water resistant material (when suitably reinforced and of sufficient depth). There is an interesting article concerning the ability of concrete to resist penetration versus concrete containing waterproofing additives, by former past president of the Concrete Society, Bob Cather.
I also attended a seminar put on by the Concrete Centre in relation to the publication of a new guide called 'Concrete Basements', where one of the Authors (Professor R.S. Narayanan BEng(Hons) MSc DIC FREng FIStructE FConsE) gave a presentation stating that "concrete is inherently watertight, magic potions (additives) are not required to make it watertight!"
While you might assume therefore that concrete is the answer to all our prayers, concrete structures still leak, including where waterproof additives are employed. A particular reason for this is that concrete structures are not formed or cast in one pour, they are poured in sections, which results in joints between elements, and these are a typical point of penetration (service penetrations and cracking being other relevant considerations).
I point this out because thinking about the joints (or any penetration through a structure) is a relatively simple way in which you can assess the resistance to water of any given structure.
I would stress at this point that the resistance of water that a given structure provides, is not the be-all-end-all and is just one consideration which has specific influences when considering certain types of waterproofing system. I can't really comment on those considerations unless we understand the impact of structure, and hence this blog post.
Coming back to joints, if we think about reinforced masonry as an example (the block/concrete/block wall type), each mortar bed in-between each block, is a joint. Furthermore the concrete element is often not particularly deep (circa 150mm) with one layer of steel (not always but this is common).
When placing concrete into the cavity between the blocks, it is not a case of filling the wall right up to the top in one go, since the weight of the 'liquid' concrete exerts a pressure, which would likely blow the masonry shuttering or push one leaf over. As a result, the walls are filled up in 'lifts', i.e. fill partially and wait for a degree of cure before filling higher, and what does this create? That's right, joints between pours.
So what sort of resistance to penetration does reinforced masonry provide..? Very little. Often these structures are treated with external barrier tanking systems in isolation, which are designed to exclude water. I've dealt with so many failures using this method on this structure, simply because the structure is permeable, and as a result there is more or less total reliance on the tanking to exclude water. These tanking systems cannot reasonably be considered to be constructed defect free (as per BS8102) and they then leak as a result if and when pressure is allowed to come to bear.
While I fully expect the design of external tanking installed in isolation on reinforced masonry to disappear in time because of the issues with this approach, at least it illustrates the impact of a permeable structure with that method.
Another example is ICF (insulated concrete formwork). The structure in this case is essentially reinforced concrete, however there is always a joint between walls and raft slab, and in addition, the inner and outer layer of polystyrene is tied together usually with a plastic, or metal tie. The implication of this is that there are a great many penetrations which run through the concrete wall, and these provide a potential pathway for penetration.
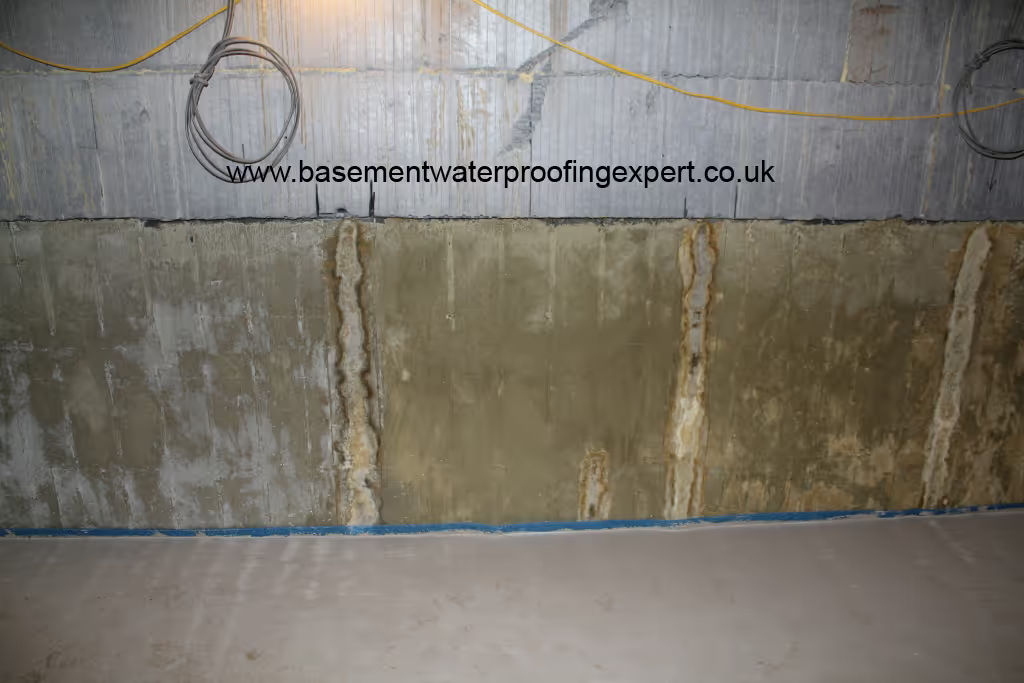
So there you have it, a few examples of structures and the considerations which influence permeability.
For the record, I happily treat and guarantee reinforced masonry and other 'permeable' structures on a constant basis, it is just a case of understanding these implications and designing appropriately (using the right products and systems) to accommodate the properties of the structure. This is achievable when you can pick and choose from a wide variety of systems. If anyone tells you anything other than reinforced concrete is a poor choice, they are probably selling a system reliant on the use of reinforced concrete. It is not about selling product, it's about creating dry basements.
At the time of writing I'm dealing with one precast concrete basement system with penetration issues, and I've just finished a remedial scheme to a BBA certified waterproof concrete admix. structure. It is a complicated field in some respects and this is where employing
experienced qualified designers/installers to take design responsibility, and experienced installers to install - is the ideal