Basement & Cellar Conversion
At Trace we are certainly passionate about the creation of awesome living spaces below ground, but we also understand the importance of delivering a space that will stay dry, backed by all of the necessary correspondence to deliver a return on the investment if and when the property is sold on.
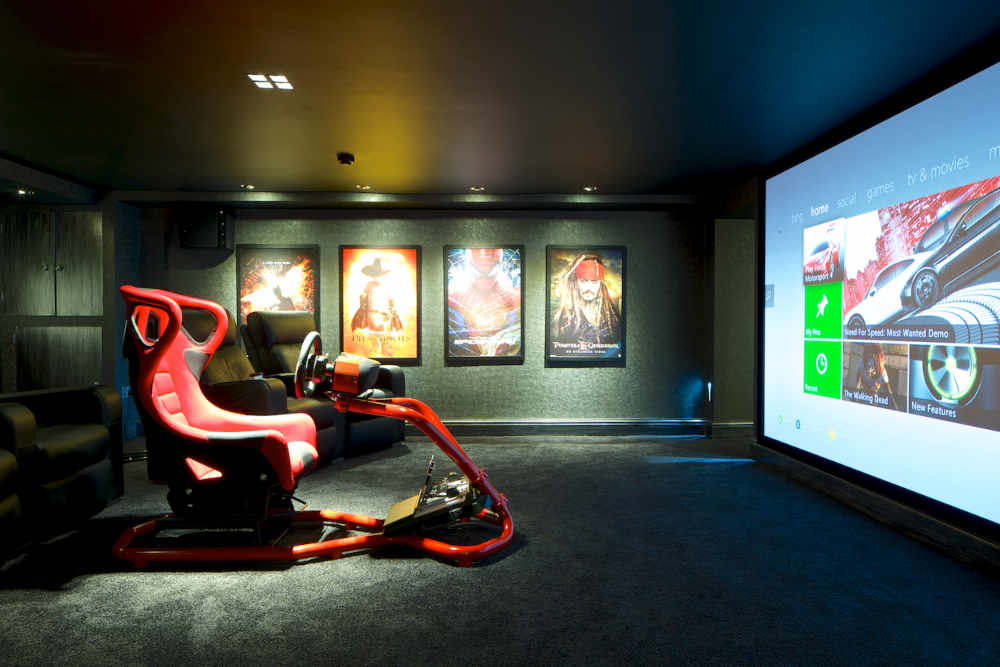
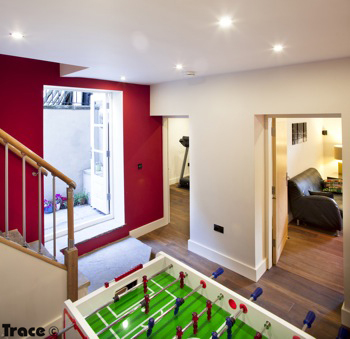
Think about your Basement Conversion long term
Basement and cellar conversions provide additional living space, and further to this, they are sometimes promoted in what might be considered as a somewhat glitzy fashion. It’s fine to get excited about the finishes, and the additional space, but a successful basement and cellar conversion starts with the waterproofing.
Waterproofing basements facilitates and preserves the conversion, allowing enjoyment of the space, and it ensures a return on your investment as and when you sell the property.
Building Regulations
Statutory requirements for the design and construction of the living space. Conservation of fuel and power (insulation), means of escape in the event of fire, just two examples. Gaining approvals and a completion certificate from Local Authority Building Control, ensures compliance and maximises property value.
Designing your basement conversion
Quality design is key, furthermore what we term 'full service' waterproofing - we detail a comprehensive system for the right outcome, not corner cutting to achieve lowest price.
Installation
Quality waterproofing installation, fit and finish is what we value. The waterproofing is not visible, but our work is as neat as you will see.
Delivering value
A dry space must be backed up by the correspondence - reports, drawings, guarantees, insurances and record of maintenance.
Similarly, submitting the design to Local Authority Building Control, ensuring compliance and then obtaining a completion certificate to recognise the change of use to habitable space, ensures that when the property is sold, the basement is recognised and valued as a habitable space.
We do sometimes get asked to inspect existing basement conversions on behalf of clients that are looking to purchase that property. In some cases there is some sort of issue which prompts the survey. We are generally limited in what we can see because where a basement is finished, it generally hides the vast majority of the waterproofing, but there are always areas where you can get some degree of access.
If what you see is questionable, inevitably the sale falls through, because it throws the rest into doubt.
I do not want to come across as being overly negative, I just know how important it is to get it right, and prevent these sorts of situations. Then of course, you can enjoy a fantastic living space.
We come to this as qualified and experienced basement conversion specialists that have been undertaking this work since 1998.
Please contact us to discuss your basement & cellar conversion.
Approved & Accredited Waterproofing Contractors
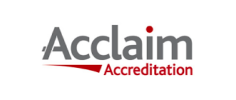
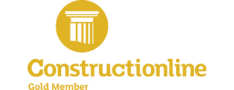
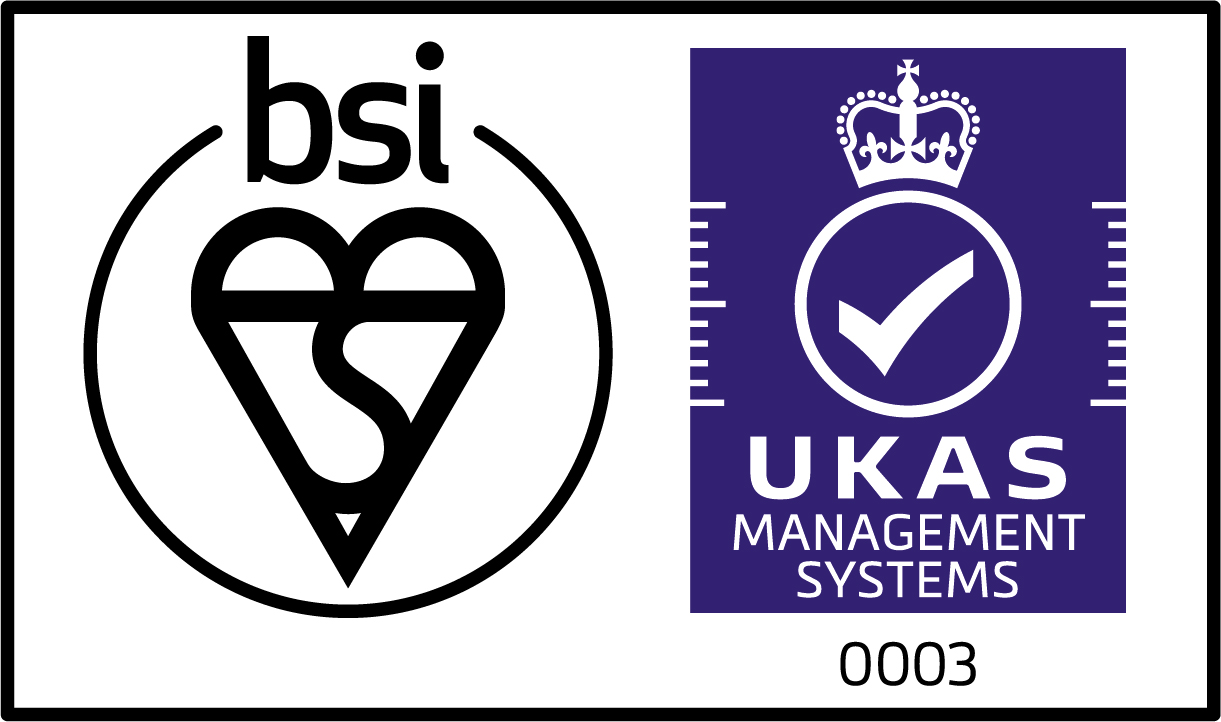
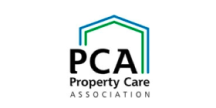
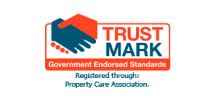
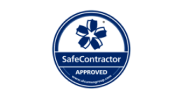
Below we include examples of recent basement and cellar conversion projects which included a variety of work from underpinning to achieve greater height, and the excavation/formation of an external stairwell & door.
While photographs tell their own story, if you have questions or wish to discuss such a project, feel free to contact us and speak with our qualified basement conversion designers.
This wall (above) was removed to form the open area including the table football, visible opposite.
<IMAGE HERE>
Below we include further advice & considerations appropriate to basement and cellar conversions:
Basement & cellar conversion is the process of taking basic basement and cellar spaces and improving the environment via the inclusion of a waterproofing system in association with heating & ventilation, so that the basement or cellar can then be employed as a habitable space.
Trace manage basement conversion in Manchester (and further afield) from design through to completion and have done so sucessfully for over twelve years. If you are interested in discussing your requirements and recieving professional advice & service, please contact us.
Trust in experience
A project completed in 2005:
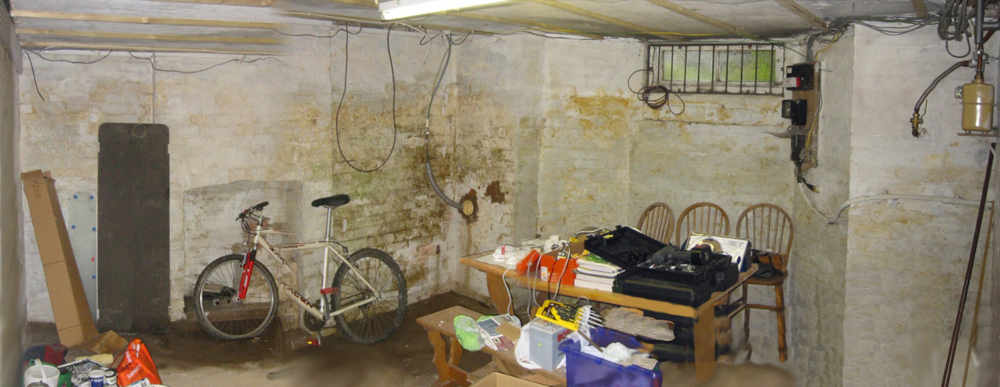
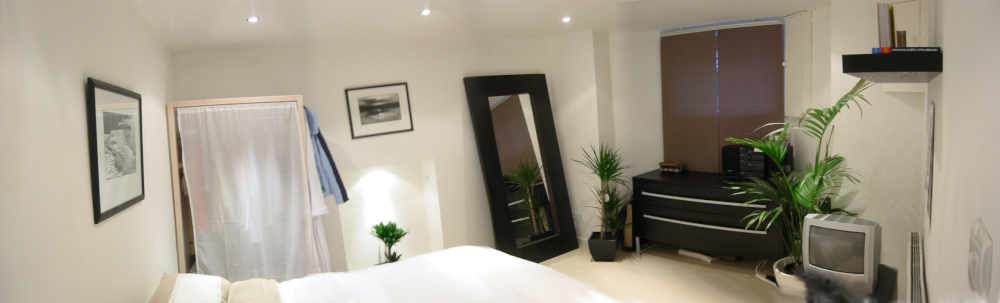
.
Award winning experts in dealing with problems of moisture in buildings. Est 1974.
.
.